Why Marine Propeller Crack Repairs Demand Precision Engineering
At Veins Marine Engineering Solution (VMES), innovation is not just a goal—it’s our identity. We are proud to share a breakthrough achievement in the history of Bangladesh’s maritime industry. VMES has successfully completed the first-ever vessel propeller crack repair in Bangladesh using Tungsten Inert Gas (TIG) welding technology. This significant development in ship propeller crack repair redefines the standard of precision marine repair in the region.
Background: The Challenge of Propeller Repairs in Marine Operations
Propellers are at the heart of vessel propulsion, enduring extreme forces, variable sea conditions, and operational stress. Over time, this exposure can result in microfractures or full cracks, severely impacting vessel efficiency, safety, and performance.
Historically, repairing cracked propellers in Bangladesh was limited to conventional arc welding or even complete part replacement—each with inherent disadvantages:
- Excessive heat distortion
- Weak fusion zones
- Imbalance in hydrodynamic performance
- High cost and time loss
Understanding the significance of ship propeller crack repair is crucial for vessel owners and operators, as it ensures the longevity and reliability of their marine assets.
VMES Breaks New Ground with TIG Welding Technology
For the first time in the country, VMES deployed TIG welding to repair a fractured marine propeller with international-standard precision. The entire operation—from damage inspection to post-repair testing—was executed by our in-house team of certified marine engineers and welding experts.
What Makes TIG Welding Superior for Propeller Repair?
TIG (Tungsten Inert Gas) welding is renowned in aerospace and critical engineering applications. Its application in maritime repairs, especially on high-load components like propellers, offers several technical advantages:
1. High-Precision Welding Control
TIG allows precise control of heat and filler material, enabling our team to target the crack without affecting the surrounding zones. This is crucial for maintaining the propeller’s aerodynamic integrity.
2. Deep Fusion with Minimal Heat Distortion
The process minimizes the heat-affected zone, ensuring no warping or imbalance—a common issue with traditional welding methods.
3. Superior Metallurgical Bond
TIG creates clean, slag-free welds with excellent penetration, which means stronger joints and longer component life.
4. Material Versatility
TIG is compatible with high-grade bronze, nickel-aluminum-bronze, and stainless-steel alloys, commonly used in modern propellers.
Execution Highlights: Step-by-Step Breakdown
- Damage Assessment & NDT Inspection
- The crack was identified through non-destructive testing (NDT), ensuring no internal flaws were overlooked.
- Pre-Welding Preparation
- Area was cleaned, ground, and pre-heated as per alloy specifications.
- A precise welding strategy was developed based on the propeller material and crack depth.
- TIG Welding Operation
- Performed under inert gas shielding (Argon) using a pulsed-current setup for improved fusion control.
- Layered passes were made for even stress distribution.
- Post-Weld Heat Treatment & Machining
- Controlled cooling and final balancing operations were completed to maintain original geometry.
- The surface was polished and protected with marine-grade anti-corrosion coating.
- Final Testing & Sea Trial Clearance
- A second round of NDT confirmed flawless results.
- The vessel successfully cleared sea trials with no vibration issues or thrust loss.
Why This Matters: Elevating Bangladesh’s Marine Engineering Capability
This project is more than just a repair—it is a demonstration of VMES’s engineering leadership in a sector hungry for reliable, localized solutions. TIG welding in marine applications is a global best practice, and VMES is proud to be the first to execute it successfully in Bangladesh.
Our ability to carry out such a repair domestically reduces:
- Downtime for vessel owners
- Foreign dependency for high-skill repairs
- Operational and logistic costs
This reinforces our commitment to making Bangladesh’s ports—including Chittagong, Mongla, Payra, and Matarbari—better equipped for advanced vessel maintenance.
Client Benefits at a Glance
- Fast Turnaround – Repair completed in significantly less time than replacement
- International Standards – Repair aligned with global Class requirements
- Long-Term Value – Extended life of existing components
- Environmental Responsibility – Minimizing waste by repairing instead of replacing
About VMES
Veins Marine Engineering Solution (VMES) is a Chittagong-based, full-service marine engineering firm specializing in:
- Propeller & shaft line repairs
- Underwater inspections
- Hull maintenance
- Custom fabrication
- Engine overhauls and more
Our team comprises certified professionals with global exposure and strong technical backgrounds, delivering results you can trust.
Get in Touch with VMES Today
Are you facing a critical vessel repair? Looking for cost-effective, high-precision marine solutions?
Let our expertise work for you.
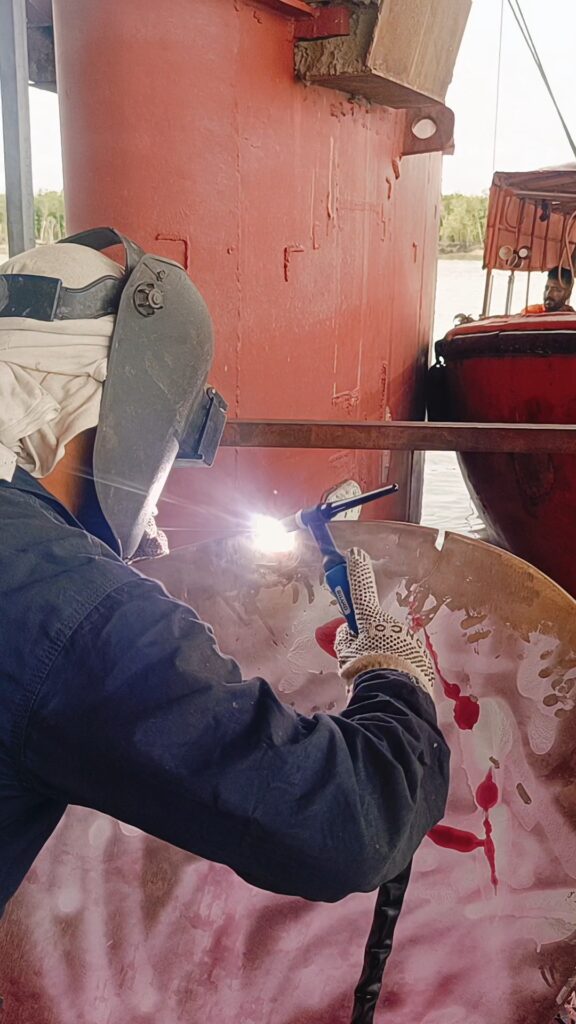
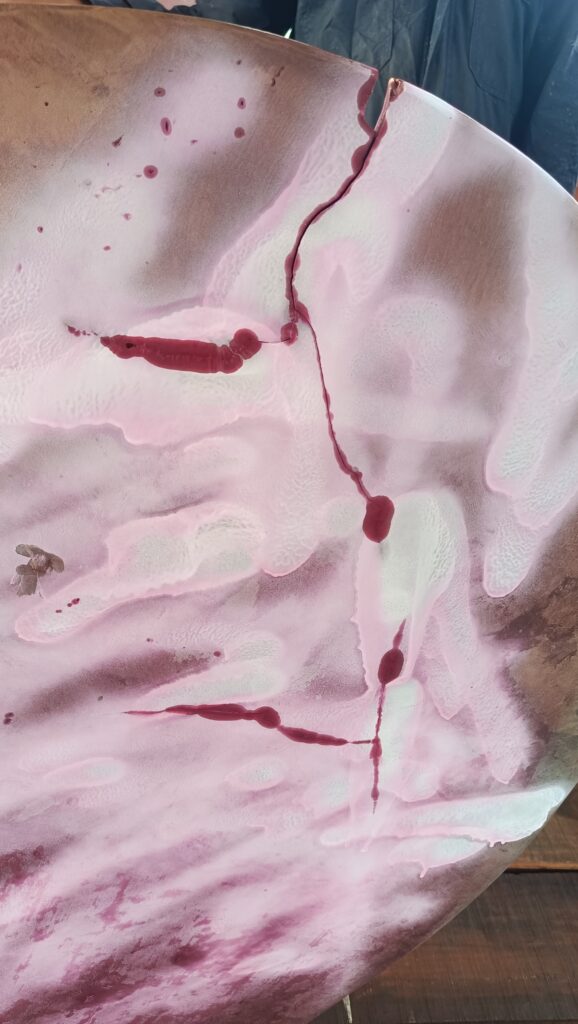
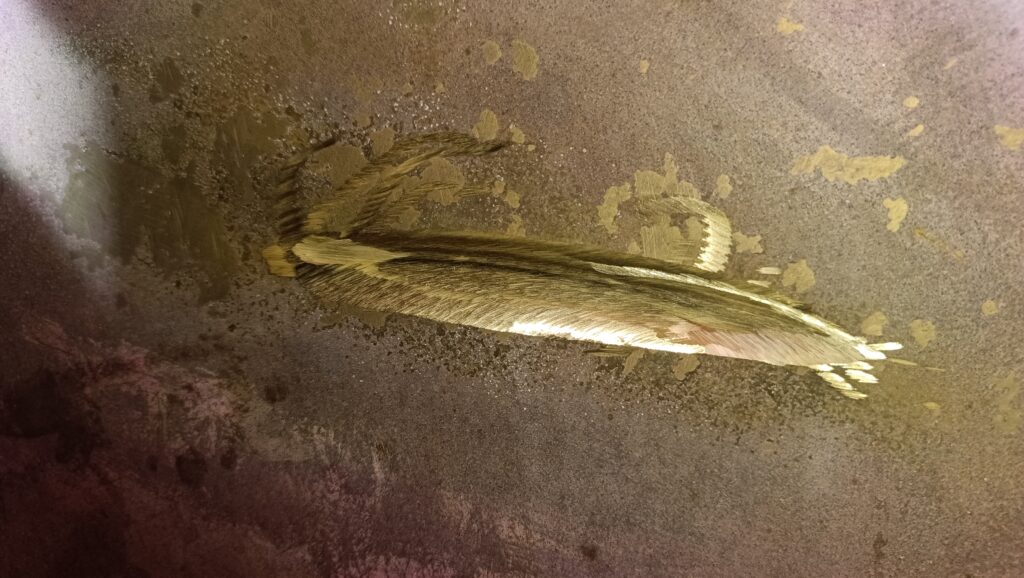

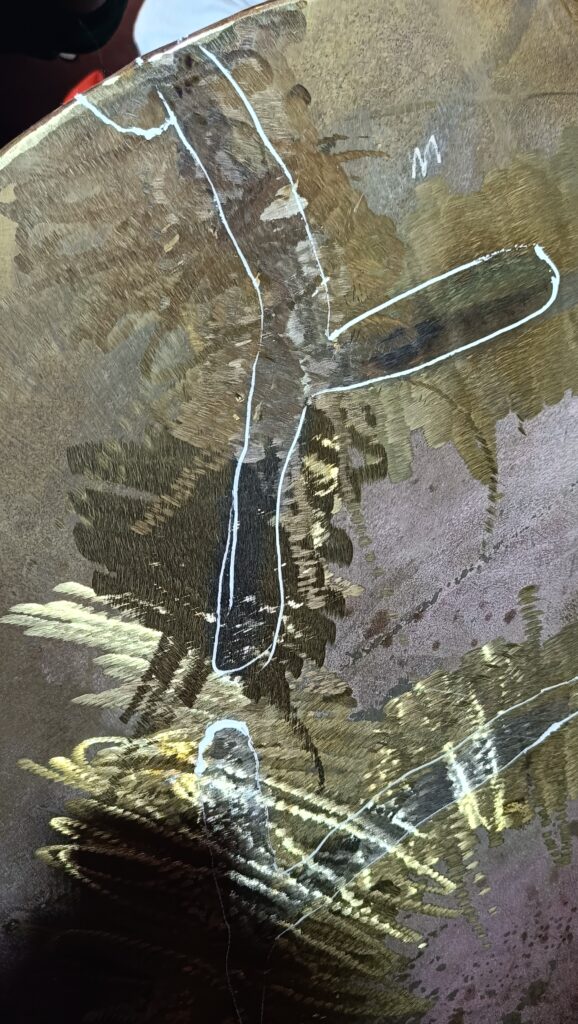
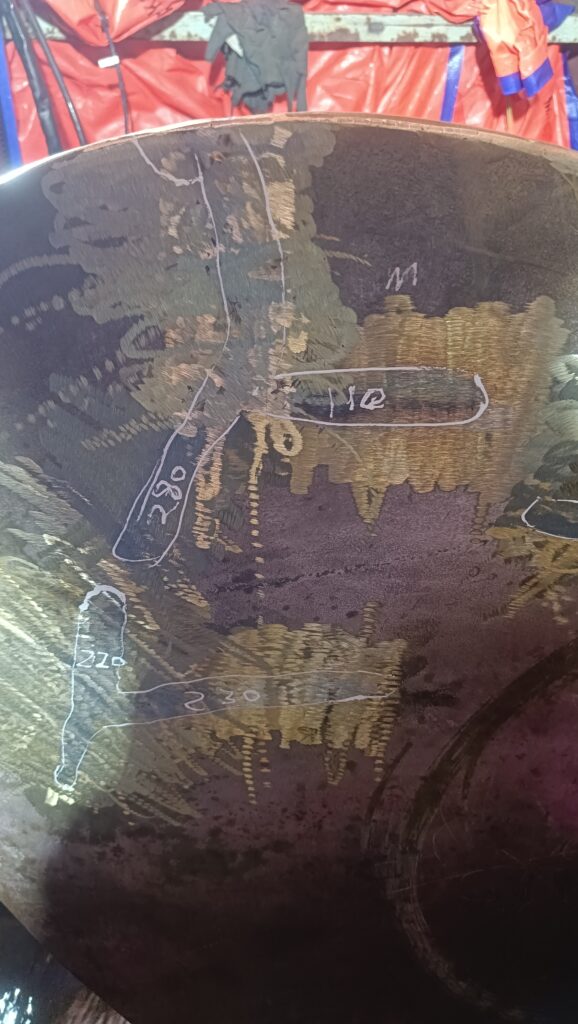